Combustible dust in the workplace, what are they and how to prevent explosions
03/03/2022

70% of the dust present in industry are flammable.
The presence of these dust within production departments can create more or less harmful explosions (depending on their nature) that occur when particular conditions are met, such as:
Most flammable dust falls into three categories:
The main parameters to determine the explosiveness of dust, and thus to know its danger in order to take the right precautions, are the following:
Combustible dusts are classified into one of four classes: St0, St1, St2, St3. The level of explosion severity increases with the class number.
A material that has a zero risk (Kst = 0) of explosion belongs to class St0.
For example, aluminium powder has a KST explosion index of 620 and is in class ST3, wheat is in class ST1 with an index of 112, and tobacco is also in class ST1 but with an index of 12.
The MIE index generally varies from 1 mJ (millijoule) to 1000mJ. The lower the MIE, the higher the risk of explosion, since even a low energy input can trigger an explosion.
In the following table, the MIE is quoted for flammable substances mixed with air. A reference is given to indicate the source of the data. MIE values are given for guidance only. Please check the references for specific measurement conditions.
For system elements such as dryers, testing the minimum ignition temperature is important to avoid a dust explosion through contact with a hot surface. The internal temperature is generally limited to two-thirds of the MIT when measured in degrees centigrade.
For example, a powder with an MIT of 450oC would require a maximum operating temperature in the drying process of 300oC, giving a safety margin of 150oC.
Equipment such as industrial vacuum cleaners, machinery and processing equipment that come into contact with combustible dust must be designed in such a way as to prevent leakage and minimise the release of dust into working areas while ensuring maximum safety.
- Vacuum cleaners for explosive dust in ATEX zones and Zone 20 indoors
- Industrial solutions for inerting conductive and explosive dust
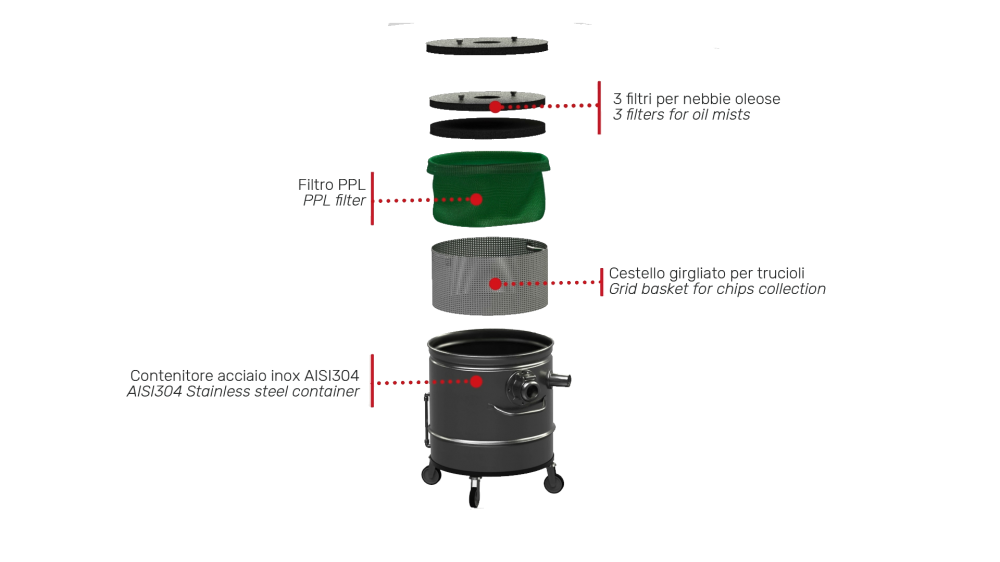
The presence of these dust within production departments can create more or less harmful explosions (depending on their nature) that occur when particular conditions are met, such as:
- The dust must be combustible;
- The dust must be dispersed in the air;
- The dust must have a particle size and distribution that makes it possible for the flame to spread;
- The concentration of the powder (in relation to the air) must be within the explosion range;
- The dust cloud must come into contact with a source of ignition;
- The dust cloud must be contained in an atmosphere capable of sustaining combustion.
Types of dust and their hazards
Most flammable dust falls into three categories:
- Natural organic materials (flour, wood, cloth, sugar, coal, cocoa powder, etc.)
- Synthetic organic materials (plastics, organic pigments, pesticides, pharmaceutical compounds, etc.)
- Metals (aluminium, magnesium, titanium, zinc, iron, etc.)
How to identify and control the explosion potential of dust
Knowing the parameters of the dust you handle in your industry is necessary to eliminate ignition sources and limit the effects of explosions while minimising injuries.The main parameters to determine the explosiveness of dust, and thus to know its danger in order to take the right precautions, are the following:
- KST
- Pmax
- MIE
- MIT
KST index
The KST index measures how destructive a given powder is once the explosion has started. It is equivalent to the maximum pressure increase in an environment under explosion conditions and is measured in bar.m/sec. The higher the Kst value, the more severe the explosion caused by the powder.Combustible dusts are classified into one of four classes: St0, St1, St2, St3. The level of explosion severity increases with the class number.
A material that has a zero risk (Kst = 0) of explosion belongs to class St0.
Dust Class | KST Value | Explosion type |
ST 0 | 0 | No explosion |
ST 1 | 1 to 200 | Weak explosion |
ST 2 | 201 to 300 | Strong Explosion |
ST 3 | >300 | Very strong explosion |
Pmax index
The Pmax index is used to calculate how much damage dust is capable of doing inside a closed environment. It is measured by increasing the concentration of dust inside a closed chamber and measuring the pressure of the explosion until the maximum is reached (to determine the maximum possible damage).MIE Index, Minimum Ignition Energy
The MIE Minimum Ignition Energy Index indicates the amount of energy required for a specific powder to ignite. Some powders require a lot of energy to ignite, while others can ignite with much less energy. When discussing explosive dust, it should be borne in mind that the MIE index is related to particle size: fine particles tend to have lower ignition energies than coarse dust.The MIE index generally varies from 1 mJ (millijoule) to 1000mJ. The lower the MIE, the higher the risk of explosion, since even a low energy input can trigger an explosion.
In the following table, the MIE is quoted for flammable substances mixed with air. A reference is given to indicate the source of the data. MIE values are given for guidance only. Please check the references for specific measurement conditions.
Material | MIE (mJ) |
Aluminium
|
50
|
Coffee
|
160
|
Potato Starch
|
20 - 25
|
MIT Index, Minimum Ignition Temperature
If a dust cloud comes into contact with a hot surface, it can self-ignite and explode. The MIT Minimum Ignition Temperature Index indicates the minimum temperature at which a hot surface will ignite a dust cloud or layer of dust after contacting it.For system elements such as dryers, testing the minimum ignition temperature is important to avoid a dust explosion through contact with a hot surface. The internal temperature is generally limited to two-thirds of the MIT when measured in degrees centigrade.
For example, a powder with an MIT of 450oC would require a maximum operating temperature in the drying process of 300oC, giving a safety margin of 150oC.
Material | MIT |
Wheat powder | 490° C |
Coal dust | No ignition up to 850°C |
Aluminium powder | 650°C |
Vacuum solutions for flammable dust
Any dust that settles on work surfaces must be removed by regular cleaning. Potentially explosive areas or equipment, including industrial vacuum cleaners, must be designed to collect dust safely and be equipped with explosion prevention systems. Delfin offers diversified solutions to suit the needs of each company:- Vacuum cleaners for explosive dust in ATEX zones and Zone 20 indoors
- Industrial solutions for inerting conductive and explosive dust
INDUSTRIAL VACUUM CLEANERS CERTIFIED FOR ATEX ZONES
ATEX industrial vacuum cleaners are built to operate in full compliance with current ATEX regulations, guaranteeing maximum operational safety, thanks to their technical characteristics:- Electrical or compressed air power supply
- Antistatic and absolute filters
- Original ATEX certified motors
- AISI 304 or 316 stainless steel construction
- Electrical components certified ATEX by the manufacturer
INDUSTRIAL VACUUM CLEANERS FOR EXPLOSIVE DUSTS ZONE 20 INTERNAL
Vacuum cleaners designed to safely handle a very high concentration of explosive dust inside the vacuum cleaner container.- Internal certification of the vacuum cleaner for zone 20
- Motors and electrical cabinet certified for Atex zones
- HEPA H14 filter on suction as standard
- Internal deflector in antistatic rubber
- Stainless steel container as standard
INDUSTRIAL VACUUM CLEANERS AND SEPARATORS WITH INERTING SYSTEM FOR CONDUCTIVE AND EXPLOSIVE DUSTS
Vacuum cleaners equipped with systems to inert explosive dusts. The material to be inerted is immersed in an oil bath that inerted it instantly, protecting both the operator and the industrial vacuum cleaner itself.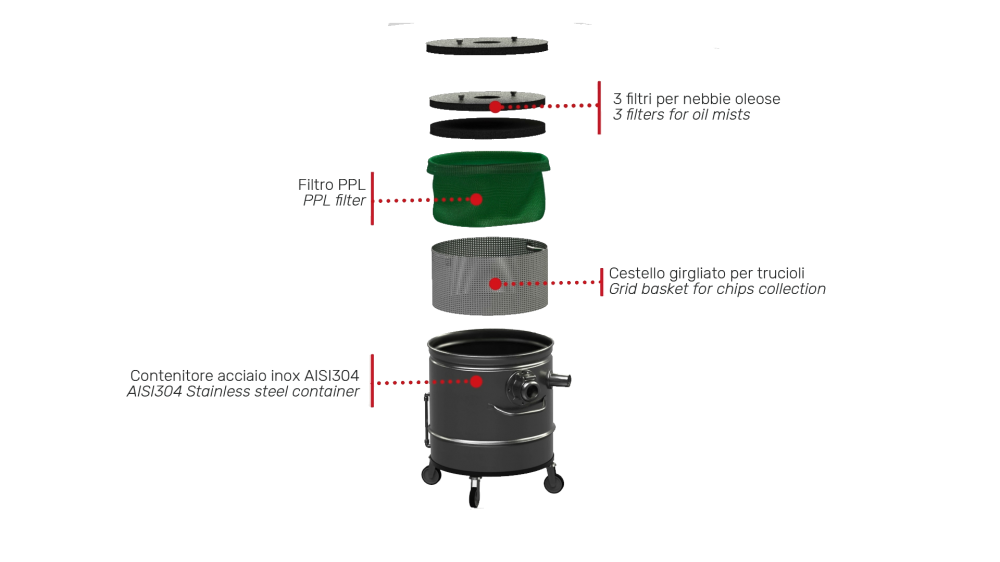